Current Situation and Prospect of Tungsten Beneficiation Research in China
Release time:
2016-07-12 00:00
1. Overview of tungsten resources
Tungsten is an important strategic metal, which is widely used in modern technology in pure metal state and alloy state. The pure metal of tungsten is silver white, with high hardness, strength and wear resistance. Alloy steel, tungsten carbide based cemented carbide, wear-resistant alloy and strong thermal alloy are the main alloy states of tungsten. Tungsten is widely used in electrical, metal rolling, mechanical processing, geotechnical engineering, aerospace, military and other fields. At present, tungsten is mainly used to manufacture cemented carbide, filament, high-speed cutting alloy steel and heat-resistant special steel, rocket thruster nozzle and firearms.
More than 20 kinds of tungsten minerals have been found in nature, and wolframite and scheelite are mainly valuable for industrial exploitation. Other tungsten minerals, such as wolframite, copper wolframite, wolframite and tungsten molybdenum lead ore, are of little industrial value.
By 2015, the world's tungsten resource reserves had reached 3.3 million tons, of which China's tungsten resource reserves had reached 1.9 million tons, accounting for 57.6% of the world's total reserves. China is the world's largest producer and exporter of tungsten resources. The tungsten resource reserves in China are concentrated, mainly distributed in 8 provinces and regions including Hunan, Jiangxi, Henan, Gansu, Guangdong, Guangxi, Fujian and Yunnan. The total proven tungsten resource reserves account for 85% of the country's total, while the tungsten resources in Hunan and Jiangxi provinces account for 50% of the country's proven reserves. Tungsten ores in China are mainly composed of wolframite, scheelite and wolframite mixed tungsten ores, among which wolframite accounts for 23.3%, scheelite for 66.9% and wolframite mixed tungsten ore for 9.8%. Tungsten ore deposit is associated with metal, nonmetal and rare earth dispersed element components, such as metal tin, molybdenum, bismuth, niobium, tantalum, lithium, beryllium, and nonmetal ore arsenic and fluorite, which have high comprehensive utilization value but low utilization rate. With the excessive exploitation and consumption of tungsten resources, the dominant position of tungsten resources in China is decreasing year by year.
2. General method of tungsten ore dressing
2.1 Scheelite beneficiation method
Scheelite (CaWO4) is composed of calcium tungstate, of which WO380.6%. Due to the brittleness and fragility of scheelite, flotation is the most commonly used separation method for scheelite at present. Scheelite ores can be divided into two types according to flotation method:
(1) scheelite quartz (or silicate mineral). This kind of ore is easy to separate. Generally, water glass can be used as an inhibitor to effectively inhibit quartz gangue, and 731 oxidized paraffin soap with strong selectivity can be used as a collector to float scheelite. A large amount of sodium silicate is added to the produced coarse concentrate, which is strongly stirred for a long time, and then diluted for concentration. This method has low ore dressing cost and is widely used in skarn scheelite mines mainly composed of quartz gangue.
(2) scheelite calcite, fluorite (barite) type. This type of ore is difficult to separate because its minerals all contain calcium and have similar floatability. This is also the key and difficult point in the flotation research of scheelite in recent years. At present, water glass and aluminum sulfate are mostly used together to improve the performance of selectively suppressing calcium gangue. Fatty acid collectors are used for rough separation. There are still a large number of fine calcite, fluorite and other gangue minerals in the obtained scheelite coarse concentrate. After the gangue minerals act with collectors, their floatability is more similar to that of scheelite, and it is difficult to separate them by conventional methods. At present, concentrated slurry high-temperature method, also known as“ Petrov method”. Its essence is to concentrate the scheelite coarse concentrate containing calcite and fluorite (the concentration is 60% - 70%), add a large amount of water glass, and strongly stir it for a long time (30-60min) at high temperature (above 80 ℃) to improve the inhibition selectivity. Petrov method has strong adaptability to ores and stable separation indexes, but it requires additional heating auxiliary equipment, with high beneficiation cost and poor labor conditions. At present, this method is widely used in scheelite mines.
2.2 Processing method of wolframite
The chemical composition of wolframite is (Fe, Mn) WO4, which is the main ore for extracting tungsten. Most wolframite ores are quartz vein type. Coarse wolframite ores are generally processed by gravity, and wolframite ores in China are mostly processed by“ Multi stage jigging&mdash& mdash; Multi stage shaker&mdash& mdash; Middling regrinding&mdash& mdash; Separate treatment of fine mud” Process flow of. The fine-grained wolframite is treated separately, and the gravity separation method is mostly used. However, the recovery rate of fine-grained wolframite is low. Therefore, the flotation research of fine-grained wolframite has begun to receive much attention. Due to the brittleness of tungsten minerals, it is easy to mud in the process of crushing and grinding, so stage grinding, stage separation, coarse grinding and early harvest, and gravity separation are often used& mdash; Flotation&mdash& mdash; The comprehensive separation process of magnetic separation combined process further improves the grade of fine wolframite concentrate.
3. Tungsten ore dressing equipment
Traditional beneficiation equipment for recovering tungsten slime includes fine slime shaker, belt chute, etc. The process of tungsten ore separation with such equipment is simple, the investment of concentrator is small, and the production cost is low. However, the plant occupies a large area, the beneficiation recovery index is not high, and the recovery effect of fine tungsten ore is poor.
The wet high intensity magnetic separator and high gradient magnetic separator have the advantages of large processing capacity and good recovery effect for fine wolframite, so they are popularized and paid attention to in the separation of wolframite slime.
The centrifugal concentrator is used for the recovery process of tungsten slime. It has the advantages of large production capacity, fine recovered ore particles, and high recovery rate of beneficiation. It is widely used in tungsten mines such as Dajishan, Pangushan, Xihuashan, etc. in Jiangxi Province.
Flotation method can effectively recover micro fine minerals, so the research of flotation equipment for fine tungsten minerals has been paid more and more attention. The ZGF-I micro bubble countercurrent contact flotation column independently developed by Hunan Zhonggong Mining Engineering Technology Co., Ltd. has the advantages of high beneficiation efficiency, low operating cost, low energy consumption, high automation, convenient maintenance, less floor area and infrastructure investment, and is widely used in tungsten mine concentrators.
Jiangxi Duchang Jinding Tungsten and Molybdenum Mining Co., Ltd. is invested by Xiamen Tungsten Industry. The construction scale of the mine is 4500 tons/day, mainly recovering tungsten and molybdenum metals. The concentrator adopts a combined column machine process, and a total of 6 ZGF-I micro bubble countercurrent contact flotation columns manufactured by CAMC are used as roughing and concentration equipment. The molybdenum content of the raw ore is 0.03%. The flotation column is used for roughing and concentration. The molybdenum concentrate grade obtained through on-site production and commissioning is 45%, and the recovery rate is 75%; The raw ore contains 0.18% tungsten, and 50-55% tungsten concentrate can be obtained by roughing and scavenging with flotation column, and the recovery rate of concentrate is about 70%; According to the field production situation, 56% energy can be saved by using flotation column instead of flotation machine.
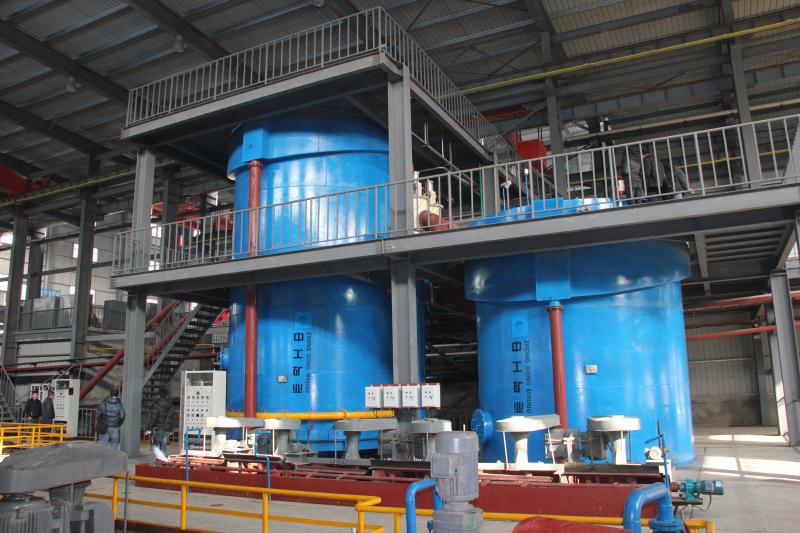
Fig. 1 Concentrator of Jiangxi Duchang Jinding Tungsten Molybdenum Mining Co., Ltd
Ninghua Xingluokeng Tungsten Mine Co., Ltd. is a holding subsidiary of Xiamen Tungsten Industry, with a production scale of 5000t/d. The average grade of raw ore is WO3 0.2%. The main process of production is one-stage grinding and graded gravity concentration; The main process production index has reached the design requirements. Primary and secondary tungsten slime (-0.043mm grain size) accounts for about 25% of the primary ore amount, with more than 1250 tons of fine slime per day. The average grade of WO3 in fine mud is 0.16%. There are many kinds of tungsten slime minerals, with low tungsten grade, wolframite and scheelite mixed, and the proportion of primary ore and weathered ore varies greatly, resulting in high recovery cost and difficult recovery technology. The ZGF-I micro bubble countercurrent contact flotation column manufactured by CAMC is used for the transformation of the beneficiation process. The flotation machine process originally used on the site was one coarse and one fine with three sweeps. After the transformation, the flotation column process is one coarse and three sweeps. The tungsten grade of the raw ore is 0.15%~0.18%. After the flotation column separation, the grade of concentrate WO3 is increased from 14%~15% to 15%~18%, and the recovery rate is increased by about 9%.
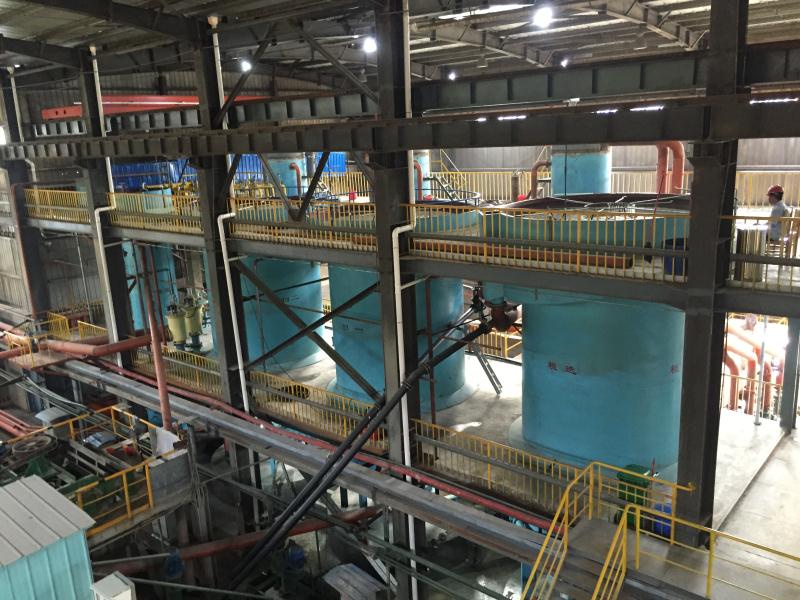
4. Tungsten beneficiation reagent
In view of the low recovery rate of tungsten slime, mineral processing researchers hope to achieve effective recovery of tungsten slime through flotation. However, the problem of flotation reagents must be solved when using flotation method to treat tungsten slime.
4.1 Scheelite flotation reagent
Scheelite has good floatability, and the separation technology and process are relatively mature, mainly including heating method and normal temperature method. The main problem to be solved in the separation process is the separation of calcium containing gangue minerals with similar floatability. The research of scheelite beneficiation reagents focuses on efficient collectors and inhibitors.
Scheelite collectors mainly include anionic collectors, cationic collectors (such as amines), amphoteric collectors (such as amino acids) and non-polar collectors, and the most commonly used is anionic collectors. There are many kinds of anionic collectors, such as fatty acid collectors, sulfonic acid collectors, chelating collectors, hydroxamic acids, phosphonic acids, etc. Commonly used industrial scheelite collectors include 733, 731, oleic acid and modified products, benzohydroxamic acid, etc. During the use of anionic collectors, in order to improve their collection performance, they usually use mixed drugs to play a synergistic effect between agents.
The flotation inhibitors of scheelite can be divided into inorganic and organic ones. Silicate and phosphate are commonly used inorganic inhibitors, such as sodium silicate, sodium hexametaphosphate, phosphoric acid, sodium polyphosphate, etc. In addition to restraining gangue minerals, water glass can also disperse slime, so it is widely used in concentrators. Organic inhibitors include macromolecular and small molecule inhibitors, and macromolecular inhibitors include CMC, tannin, pyrogallic acid, starch, etc., which can be used to inhibit gangue minerals such as quartz, calcite, fluorite, etc. Small molecule inhibitors include oxalic acid, tartaric acid, citric acid, lactic acid, etc. The solubility is better than that of large molecule inhibitors.
4.2 Wolframite flotation reagent
The research of wolframite flotation reagents mainly includes wolframite flotation collectors and regulators. The collectors for wolframite flotation mainly include fatty acids, including oleic acid and its soaps, such as oxidized paraffin soap, refined tall oil, sulfonated carboxylic acid, etc; Hydrocarbon phosphonic acids, including high-grade alkyl phosphonic acid, styrene phosphonic acid, etc. Phosphonic acids can not be used as wolframite slime flotation with calcite as the main gangue; Alkyl arsonic acids, including toluenesulfonic acid, benzyl arsonic acid, higher alkyl arsonic acid, etc. The collecting ability of arsonic acid collectors for calcite is weaker than that of phosphonic acids, so the selectivity is better than that of phosphonic acid when calcite is used as the main gangue in flotation, but arsonic acid is toxic to some extent, causing great environmental pollution and tends to be eliminated; Hydroxamic acid chelating agents include benzohydroxamic acid, salicylhydroxamic acid, etc. The collection performance of hydroxamic acid is equivalent to that of phosphonic acid, but its toxicity is much less than that of arsonic acid.
At present, the effective activators for tungsten ore flotation are lead nitrate and ferrous sulfate. Lead nitrate has obvious activation effect on wolframite and scheelite, and ferrous sulfate also has certain activation effect on wolframite.
The most common gangue mineral inhibitors in tungsten mineral flotation operations are water glass, carboxymethyl cellulose (CMC), starch, sodium fluosilicate, sodium hexametaphosphate, etc.
5. Prospect of tungsten beneficiation technology
According to statistics, the metal content in tungsten mineral slime accounts for 11% of the metal content of raw ore— 14%, and the recovery rate of fine mud accounts for 3% of the total recovery rate— 8%, effectively improving the recovery rate of fine mud is very important to improve the comprehensive recovery rate of tungsten and the economic benefit of the mine. Therefore, under the situation that the mining industry has entered the adjustment period, we should strengthen the research and development of tungsten beneficiation technology and treat the development of tungsten mining industry with a scientific and sustainable development view. Tungsten ore dressing needs to strengthen research in the following aspects:
(1) Pay attention to the process mineralogy research of the ore, fully understand the mineral composition and mineral distribution of the ore, and provide a basis for the tungsten concentrator to determine a reasonable beneficiation method and process flow.
(2) Strengthen the research of tungsten slime separation technology to improve the recovery rate of tungsten slime minerals.
(3) Strengthen the research and development of beneficiation equipment of tungsten concentrator, such as new gravity separation equipment and flotation equipment, to achieve effective separation and recovery of fine slime tungsten minerals.
(4) Strengthen the research and development of tungsten ore dressing reagents, develop tungsten ore dressing reagents with low pollution, low cost and high efficiency, and improve tungsten ore dressing process indicators.