Four types of fluorite ores and their beneficiation methods
Release time:
2016-09-19 00:00
Distribution of fluorite resources
Fluorite, also known as fluorite, is mainly composed of CaF2, with a relative density of 3.0 ‐ 3.2, a Mohs hardness of 4, a brittle property, and a melting point of 1270-1350 ℃. Fluorite is a common mineral, which is widely distributed. According to the statistics of the United States Geological Survey in 2015, the fluorite mineral resources identified globally are about 500 million tons, and the reserves identified are about 250 million tons. China's fluorite reserves rank the third in the world, second only to South Africa and Mexico.
Table 1-1 Global Fluorite Production and Reserves
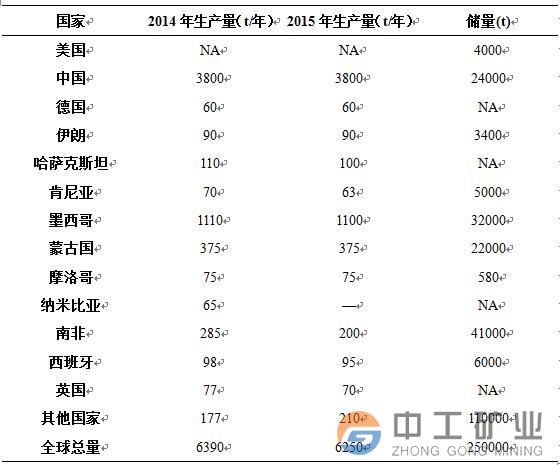
China's fluorite resources are generally more in the east and less in the west, and more in the south and less in the north. They are distributed in 27 provinces (regions) nationwide, but concentrated in Hunan, Zhejiang, Mongolia, Jiangxi, Fujian, Henan and other provinces. There are many single type fluorite deposits and few reserves in China; The number of concomitant deposits is small but the reserves are large. In a single fluorite ore, the grade of CaF2 is generally 35%— 40%, of which the reserves of fluorite ore with a grade greater than 65% that can be directly used as metallurgical grade rich ore only account for 20% of the total reserves of a single fluorite deposit. The grade of CaF2 in fluorite ore associated with metal deposit is generally only 7%— 20%。 Although the associated fluorite deposit has a large amount of resources, its grade is relatively low, and it is often comprehensively recycled during the mining of the main ore species. China's large and medium-sized fluorite mining areas include Wuyi, Zhejiang, Shizhuyuan, Hunan, Jiang'an, Hebei, De'an, Jiangxi, Sumo Chagan Aobao, Inner Mongolia, Qinglong Dachang, Guizhou, etc.
Current utilization of fluorite
Fluorite is widely used as a strategic non-metallic raw material. Fluorite can be divided into three categories according to its grade and use: (1) acid grade fluorite used in the chemical industry, with a fluorite mass fraction of more than 97%; (2) Metallurgical grade fluorite used for steelmaking and aluminum electrolysis, with a mass fraction of 65% fluorite; 85%; (3) The ceramic grade fluorite used for making glass and ceramics in the building materials industry has a mass fraction of 85% - 95%. At present, the main consumption structure of fluorite in China is steel making accounting for 13%, aluminum making accounting for 8%, fluorine chemical industry accounting for 29%, cement and glass industry accounting for 40%, and others accounting for 10%. Hydrofluoric acid is the key intermediate product of fluorite and other fluoride resources to realize chemical deep processing and develop fluoride chemical industry. With the rapid development of China's fluorine chemical industry, more and more acid grade fluorite resources are needed.
Type of fluorite ore and its beneficiation method
According to the different gangue minerals, fluorite ore can be divided into four types, namely quartz type fluorite ore, carbonate type fluorite ore, barite type fluorite ore and sulfide type fluorite ore.
(1) Quartz type fluorite ore: the main minerals are fluorite and quartz, and the fluorite content can reach 80% - 90%. It contains a small amount of calcite, barite and sulfide.
(2) Carbonate type fluorite ore: the main minerals are fluorite and calcite. The content of calcite can reach more than 30%, with a small amount of quartz, sometimes constituting quartz calcite fluorite type ore.
(3) Barite type fluorite ore: the main minerals are barite and fluorite, and the content of barite is 10%~40%. This type of ore is often accompanied by pyrite, galena, sphalerite and other sulfides, and sometimes the content of quartz increases, forming a quartz barite fluorite type ore.
(4) Sulfide type fluorite ore: its mineral composition is basically the same as that of quartz fluorite, but it contains more metal sulphides, and sometimes the lead and zinc content can reach industrial grade.
For quartz type fluorite ore, it is mainly to reduce silicon in concentrate. For fine grained quartz type fluorite ore, oleic acid or oxidized paraffin soap is generally used as the collector, sodium carbonate as the slurry pH regulator, and sodium silicate as the inhibitor. The process flow of stage grinding and stage separation is adopted, and high-quality fluorite concentrate can be obtained after multiple cleaning.
For carbonate type fluorite ore, because fluorite and calcite both contain calcium ions and their solubility is similar, there is mutual transformation between minerals when they coexist in solution, which makes it difficult to separate fluorite and calcite. Generally, water glass or salinized water glass or acidified water glass is used to inhibit carbonate, oleic acid or other fatty acids as the collector of fluorite; Both calcite and fluorite can be well collected by oleic acid in the pH range of 8~9.5. Inhibitors should be used to adjust the floatability difference of these two minerals, so as to realize the separation of the two minerals.
For the barite type fluorite ore, because the floatability of barite and fluorite is similar, the separation of fluorite and barite is also a difficulty in the fluorite flotation process. Generally, sodium carbonate is used as the adjusting agent, water glass as the gangue inhibitor, and oleic acid as the collector. The mixed concentrate of fluorite and barite is obtained by mixed flotation, and then the mixed concentrate is separated by fluorite and barite flotation. There are two methods to separate fluorite from barite: one is to inhibit the flotation of fluorite from barite, and the other is to inhibit the flotation of barite from fluorite. It is found that trivalent cations such as Al3+and Fe3+can inhibit barite and activate fluorite, whereas bivalent barium salt and lead salt can activate barite and inhibit fluorite.
For sulfide type fluorite ore, xanthate or black powder is used to first float sulfide, and then fatty acid collectors are used to float fluorite concentrate.
Conclusion
China is rich in fluorite resources, but the average grade is low and it is difficult to separate. In terms of fluorite ore dressing, stage grinding, stage separation and multiple concentration are the main flow of fluorite flotation. However, this process has some shortcomings, such as complex structure, large floor area and large energy consumption. Therefore, simplifying the structure of beneficiation process and exploring new flotation process and flotation equipment are important research directions for fluorite separation. Flotation column has high beneficiation efficiency and large enrichment ratio; Simple equipment structure and process flow; Small floor area, low equipment investment cost; It has been successfully applied in many fluorite mines at home and abroad, and is a new energy-saving equipment with broad application prospects.