Beneficiation test of fine fluorite by micro bubble countercurrent contact flotation column
Release time:
2016-09-28 00:00
Fluorite, also known as fluorspar, is mainly composed of CaF2 with a relative density of 3.0 ‐ 3.2. Fluorite is a common mineral, which is widely distributed. According to the statistics of the United States Geological Survey in 2015, the fluorite mineral resources identified globally are about 500 million tons, and the reserves identified are about 250 million tons. China's fluorite reserves rank the third in the world, second only to South Africa and Mexico. As a strategic non-metallic raw material, fluorite is widely used in chemical industry, building materials, ceramics, metallurgy and other fields. With the gradual shortage of high-quality fluorite resources, it is of great significance to carry out beneficiation test research on fine fluorite with low raw ore grade and complex embedded particle size.
Ore properties
The fluorite ore selected by the concentrator is mica fluorite metasomatic rock. The fluorite is surrounded by calcite, sericite and other impurity minerals, which are in the form of stars or even stars; Local chalcedony or limonite are filled with metasomatism, and calcite or sericite are often filled in the small corrosion holes of fluorite that are arranged directionally along the cleavage plane, so even coarse crystalline fluorite is not pure, and often contains fine fine calcite inclusions; It is difficult to dissociate fluorite mineral monomer and obtain high grade concentrate products. The multi-element analysis results of raw ore are shown in Table 1-1, and the mineral composition of raw ore is shown in Table 1-2. The main mineral composition is fluorite, mica, calcite, and the main valuable mineral is fluorite.
Table 1-1 Multi element Analysis of Raw Ore
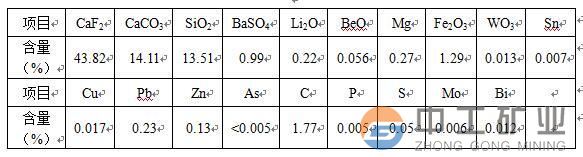
Table 1-2 Relative Content of Main Minerals in Raw Ore
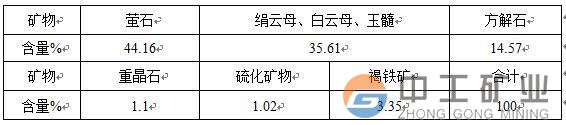
The embedded particle size of fluorite determined under the thin section microscope of ground raw ore block is shown in Table 1-3. The proportion of fluorite less than 40 microns is about 14%, and fine grinding can fully dissociate fluorite.
Table 1-3 Embedded particle size of ore
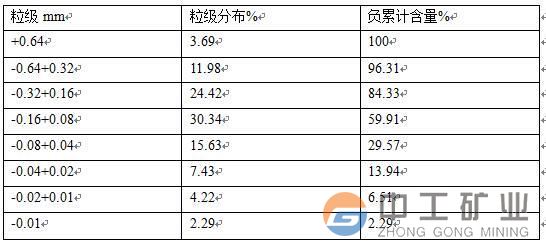
Working principle of microbubble countercurrent contact flotation column
The ZGF-I microbubble countercurrent contact flotation column developed by Hunan Zhonggong Mining Engineering Technology Co., Ltd. is a new type of highly efficient non mechanical stirring aerated flotation equipment. The flotation column consists of five parts, mainly including: column, ore feeding system, gas supply system, automatic control system, tailings discharge system, etc. The structure diagram is shown in Figure 1 below: the air compressor generates high pressure and high speed air flow, which is injected into the column through the foam gun installed at the bottom of the column; The gas jet produces a large number of micro bubbles, and the ore particles and bubbles are in steady contact with each other in the counter current in the column, and the hydrophobic ore particles are captured to float upward to form foam concentrate; Unfloated minerals are discharged through tailing valve; The liquid level and the thickness of foam layer are adjusted by the liquid level control system.
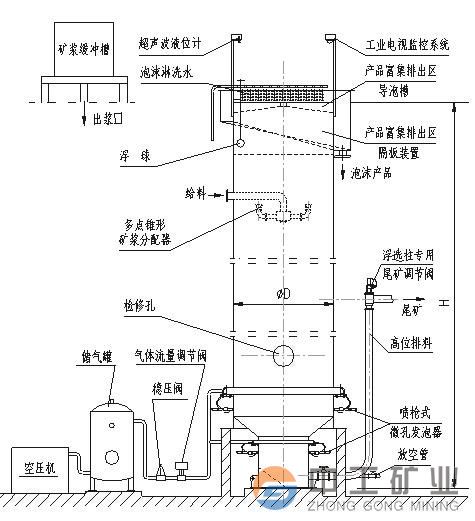
ZGF-I micro bubble countercurrent contact flotation column has high recovery of fine minerals; The energy saving effect is remarkable. Compared with the traditional flotation machine, it can save more than 30% electricity; The foaming gun can be replaced by current carrying, and the wearing parts are easy to maintain; High degree of automation and stable operation; It has the advantages of less land occupation and capital construction investment.
Results and analysis of flotation column test
The test is mainly to conduct flotation column flotation test on the cleaned fluorite ore and cleaned tailings. A part of the pulp is directly diverted from the field flow and enters the flotation column test system. The test reagent system is consistent with the on-site reagent system.
Comparison between the test results of combined separation of fluorite coarse column separator and field indexes.
After the raw ore is cleaned, it is grinded by two stages and two closed circuits— The classification process enters the roughing system, and the combined process of one roughing and one column sweeper is used. The flotation column is used for roughing, and the flotation machine is used for scavenging. The pulp concentration is 16%— 20%, with grinding fineness of - 325 mesh accounting for 85%. Setting of flotation column test parameters: the ore feeding rate is 2.5 L/min, the thickness of the flotation column foam layer is 20 cm, and the inflation rate is 0.55 L/min. See Table 3-1 for test results.
Table 3-1 Fluorite roughing test results and indicators on duty

The results of fluorite roughing test show that the average grade of fluorite is 81.47% and the average recovery is 88.61% by using the column machine combined process; The statistics of the indicators for the on-site shift production of this type of ore show that the average grade obtained by the full flotation machine process is 80.42%, and the average recovery rate is 84.81% of the grade of coarse concentrate; The average grade of the coarse concentrate obtained in the test is 1.05% higher than the actual one, and the average recovery is increased by 3.8%. It can be seen that the column machine combined process can obtain higher grade fluorite coarse concentrate than the full flotation machine process, and the recovery rate is also improved.
Comparison of flotation column test results of fluorite recovered from concentrate tailings with field indexes
In the production process, the fluorite concentrate is obtained from the fluorite coarse concentrate through the flotation process of one roughing, one scavenging and six finishing, but the tailings loss is relatively serious, and the fluorite content in the cleaned tailings reaches 40%~62%; At the same time, the viscosity of the foam scraped from the flotation cell is high, which requires a lot of flushing, resulting in a very low concentration of tailings, only 4%~8%; The concentrator adopts the process of one roughing, one scavenging and two refining to recover this part of tailings after its concentration, but the flotation recovery effect is not ideal. Therefore, it is considered to adopt the combined flotation process of one rougher and one column sweeper to conduct fluorite recovery test on the cleaned tailings. The parameters of the flotation column are designed as follows: the ore feeding rate is 2.5 L/min, the thickness of the foam layer of the flotation column is 25 cm, and the inflation rate is 0.5 L/min; See Table 3-2 for test results.
Table 3-2 Flotation Test Results and Shift Indexes of Concentrated Tailings
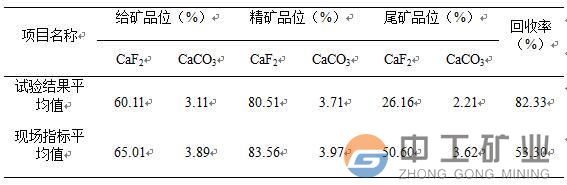
The flotation test results of fluorite recovered from concentrate tailings show that the average grade of fluorite concentrate can be 80.51% and the average recovery rate is 82.33% after the combined flotation process of one roughing and one column sweeping machine; Compared with the field production index, the concentrate grade obtained in the test is 3% lower, but the operation recovery rate has been greatly improved, with an average increase of 29%, and the total recovery rate of fluorite can be increased by 5%~8%.
Conclusion
1. The analysis of ore properties shows that the metasomatic symbiosis of fluorite minerals and impurity minerals in the ore is complex, the particle size of minerals is uneven, and the monomer dissociation is difficult; At the same time, the ore contains large amount of mud and high content of viscous substances, which worsens the flotation environment; Therefore, it is difficult to obtain high grade fluorite concentrate by flotation.
2. The flotation column test results show that the average grade of the coarse concentrate obtained in the test is 1.05% higher than the site index, and the average recovery is 3.8% higher than the site index by using ZGF-I micro bubble countercurrent contact flotation column for fluorite roughing; In the flotation test of recovering fluorite from concentrate tailings, the operation recovery rate of fluorite is increased by more than 20%, which can finally increase the total recovery rate of fluorite by 5%~8%.
3. The flotation column test results show that the column machine combined process can obtain higher grade coarse fluorite concentrate than the full flotation machine process, and can significantly improve the recovery rate of fine fluorite in the cleaned tailings. ZGF-I micro bubble countercurrent contact flotation column generates a large number of micro bubbles through the foaming gun, improving the probability of collision and adhesion between bubbles and fine fluorite, and improving the recovery effect of fine fluorite minerals.