How to Select Flotation Equipment Reasonably
Release time:
2016-09-30 00:00
The most basic link of concentrator construction is beneficiation test. The beneficiation test is the most important basis for evaluating whether the mineral resources have commercial mining value. Before determining the mine investment and plant construction, it is necessary to conduct beneficiation test research to minimize the investment risk.
Through the beneficiation test, a reliable basis is provided for the design of the concentrator. The properties of different types of ores in different regions are ever-changing, and the beneficiation methods, technological processes and technical conditions are also different. The best technological process can only be determined through beneficiation test.
According to the best process flow recommended by the beneficiation test and the construction scale of the concentrator, the concentrator shall be designed, the selection of beneficiation equipment shall be calculated, and the most reasonable beneficiation equipment shall be selected, so as to ensure that the construction investment of the concentrator is small, the speed is fast, the production is early, and the standard is reached, and finally the goal of high index, low cost, and good economic benefit is achieved.
Introduction to flotation equipment
Flotation machine
A flotation machine is a flotation device with a mechanical agitation device. It relies on the impeller to transport pulp and disperse air. Bubbles and particles collide and adhere in the collection area. Mineralized particles arrive at the foam area under the upward conveying force generated by the impeller and are discharged from the overflow weir.
It can be divided into mechanical agitation flotation machine and pneumatic mechanical agitation flotation machine according to different aeration and agitation methods.
Mechanical agitation flotation machine relies on mechanical agitation device to realize pulp inflation and agitation. The advantages of this type of flotation machine are: it can suck air and pulp by itself, without additional aeration device, and it is easy to realize self flow when the middling returns; Its disadvantages are: small at best, high energy consumption and large wear.
The aerated mechanical stirring flotation machine mixes the pulp through the mechanical stirring device, and another blower is set to provide aeration. The advantages of this type of flotation machine are: large air volume, air volume can be adjusted as required, and wear is small; Its disadvantage is that there is no suction and slurry suction capacity, and additional blower and slurry return pump are required.
Due to the working principle and mode of the flotation machine itself, the flotation column has the following characteristics in industrial application:
1. It has a wide scope of application and strong adaptability. Almost all minerals have successful application examples.
2. It has its own slurry mixing device, which can strengthen the dispersion of reagents.
3. It has strong collection capacity for intergrowth particles, which is conducive to improving the recovery rate of minerals.
4. Large floor area and high energy consumption of equipment.
Flotation column
The flotation column is an aerated non mechanical stirring flotation device with simple structure. Bubble generator is the key component of the flotation column, which directly affects the maximum and the degree of bubble dispersion as well as the working efficiency of the flotation column. Adding foam washing water in the foam area of the flotation column can reduce the entrainment of non target minerals in the foam and improve the concentrate grade. There are many kinds of flotation columns used for mineral separation in China, which can be divided into two categories according to different bubble generation modes: inflatable flotation column and gas— Liquid mixed flow flotation column.
The bottom of the inflatable flotation column is equipped with a bubble generator, and the compressed air provided by the external air source diffuses and inflates into the column through the microbubble generator. The pulp is fed from the middle and upper part of the flotation column, the mineral flows down the flow and the bubble flows up against the current, and the two collide against the current inside the flotation column.
Gas— The liquid-liquid mixed flow flotation column can create a high-speed turbulent mixing environment in the bubble generator. The pulp and air are subject to turbulent collision in the bubble generator, and then the gas-liquid mixture is injected into the flotation column. The bubbles and mineral particles are subject to countercurrent collision.
Compared with flotation machine, flotation column has the following characteristics:
1. Simple structure, convenient operation and maintenance.
2. It can reduce the number of flotation sections and simplify the beneficiation process.
3. No mixing device, low energy consumption.
4. Small floor area, low capital construction cost, etc.
The ZGF-I flotation column independently developed by Hunan Zhonggong Mining Engineering Technology Co., Ltd. is an air filled flotation device. The mineral particles and micro bubbles contact smoothly in countercurrent, which can effectively improve the recovery rate of fine minerals; The thickness of concentrate foam layer can be adjusted, and the concentrate grade can be significantly improved by the action of foam washing water. ZGF-I flotation column has been successfully applied to the separation of molybdenum ore, copper ore, tungsten ore, lead zinc ore, gold ore, fluorite, graphite and other ores. The equipment operates stably, the beneficiation index is excellent, and the energy saving effect is remarkable.
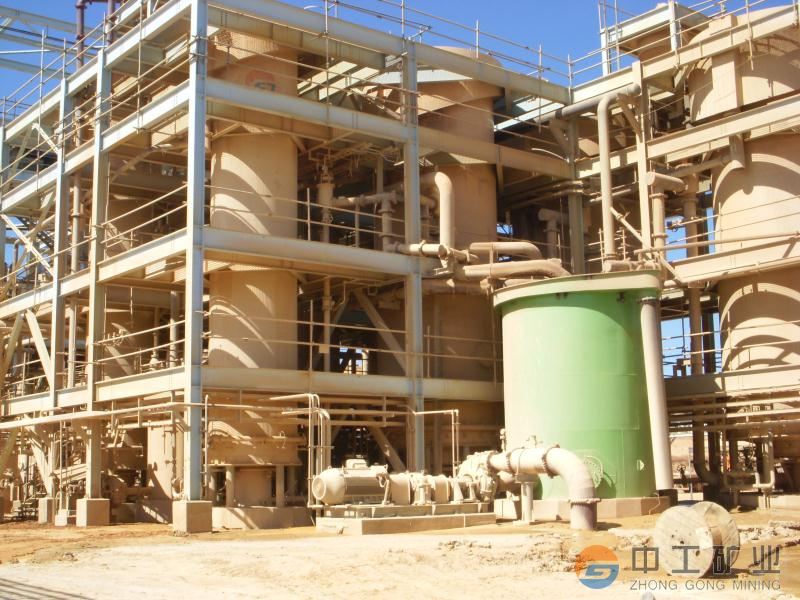
Selection of flotation equipment
The selection of flotation equipment is not only related to ore properties, grinding particle size, pulp concentration and flow structure, but also related to equipment performance, concentrator scale, series division and other factors.
1. For ores that are easy to produce viscous foam in the flotation process, flotation equipment with large inflation volume should be selected.
2. For ores with coarse particle size or high density, high concentration pulp flotation is generally used to reduce particle settling speed and particle deposition, and mechanical stirring flotation machine is preferred.
3. For the separation of ores with fine mineral particle size, long beneficiation process flow and high concentrate enrichment ratio, flotation column is preferred. The flotation column has unique advantages in the separation of fine minerals. Its high enrichment ratio provides favorable conditions for optimizing the flotation process, simplifying the process flow, and reducing equipment investment.
4. The concentration operation is mainly to improve the concentrate grade, so the use of flotation column should be given priority. The flotation column has a thick foam layer, and foam flushing water can be added, which is conducive to improving the concentrate grade.
5. The primary purpose of scavenging operation is to ensure the recovery rate of target minerals, and the flotation column should be used cautiously.
6. The specification of flotation equipment shall be reasonably selected according to the pulp flow to ensure the flotation time of pulp and the separation effect. In order to give play to the advantages of large flotation equipment, the flotation series shall be reduced as much as possible.
With the development of flotation column technology, flotation column is widely used in the separation of micro fine minerals such as nonferrous metal ores, ferrous metals and non-metallic ores; The column flotation technology and the machine flotation technology are rapidly integrating. The concentrator designer can choose to use the full flotation machine process and the flotation machine according to the characteristics of the mineral separation process and the different performances of the flotation machine and the flotation column; Combined flotation column configuration process or full flotation column configuration process, so as to achieve better technical and economic indicators.